Molybdenum Sputtering Target in PVD Method
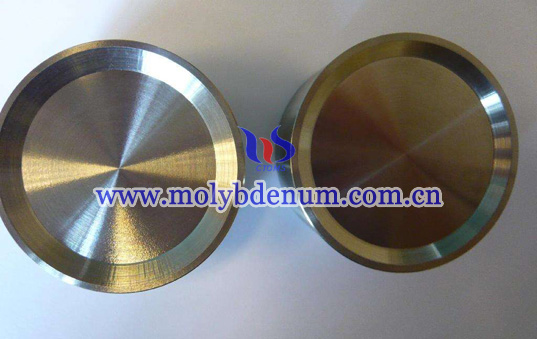
Sputtering is a PVD method for manufacturing thin films by means of evaporating solid target material (the so called sputtering target) by means of erosive plasma and depositing the evaporated target material onto the surface of the substrate forming a thin film layer. Therefore, molybdenum sputtering target is the product with balanced die distribution that can be used in PVD method to have a good test result.
The deposition source is a magnetic cathode with a metallic plate (target – made of the molybdenum that it's required to deposit) installed on it.
In the sputtering process argon plasma is ignited in a vacuum chamber and argon ions are accelerated towards a negatively charged cathode (namely molybdenum sputtering target) by means of an electrical field. The argon ions hit the target with high kinetic energy, resulting in the emission of atoms of the target material. These atoms diffuse through the vacuum chamber and condense as a thin layer on the substrate.
It's a metal deposition system originally used only on substrates with level surfaces, instead now it's applied also on tridimensional pieces but with easy shapes and structures.
The magnetic cathode is generally located on one side of the process chamber. The substrates rotate in front of the source. When is reached the required vacuum value it's set a high voltage and it's injected argon gas.
The argon positive ions are undergone to an acceleration process on the negative cathode and due to that they expel the atoms from molybdenum sputtering target.
All processes are designed to assure constant availability of molybdenum sputtering target that meets our customers' requirements. We secure the long-term availability of raw materials, constantly work to develop new product dimensions and geometries, and adapt our production capacity to our customers' volume requirements.